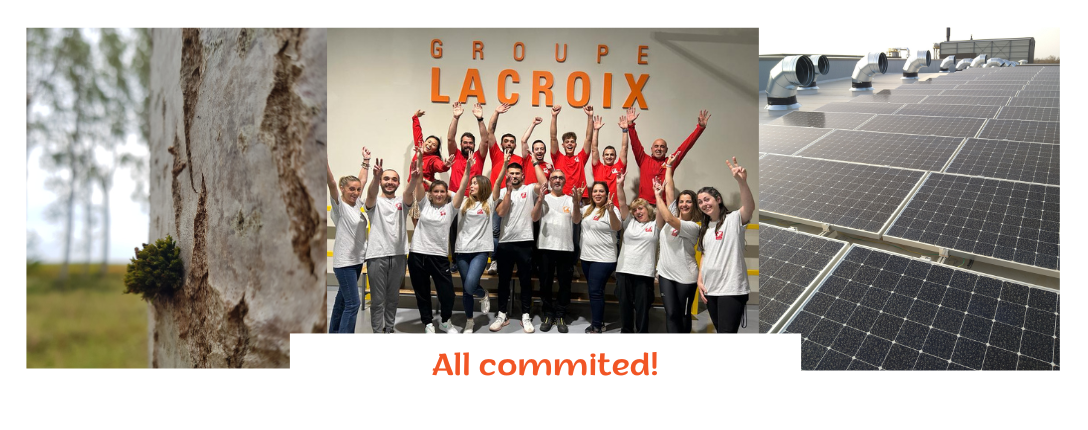
ACTING RESPONSIBLY AND ETHICALLY IS AT THE HEART OF EVERYTHING WE DO.
We have been committed to a sustainable approach for several years now. From eco-designing our packaging to optimising resources, today Corporate Social Responsibility is seen by our teams as driving innovation.
We now have 31 production sites in 11 countries, so that we are as close as possible to our customers. 65% of them have an environmental certification and we are doing everything we can to follow them on this road.
Our missions
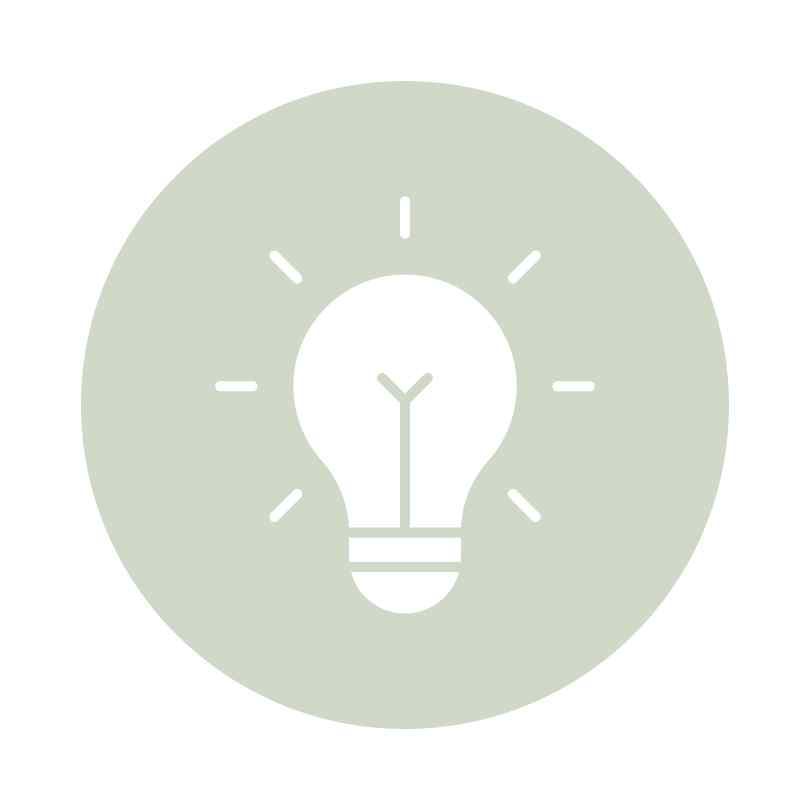
INNOVATION AND ECODESIGN. Our Development, Quality and Engineering departments have always sought out the most virtuous solutions and manufacturing methods when designing tomorrow’s packaging.
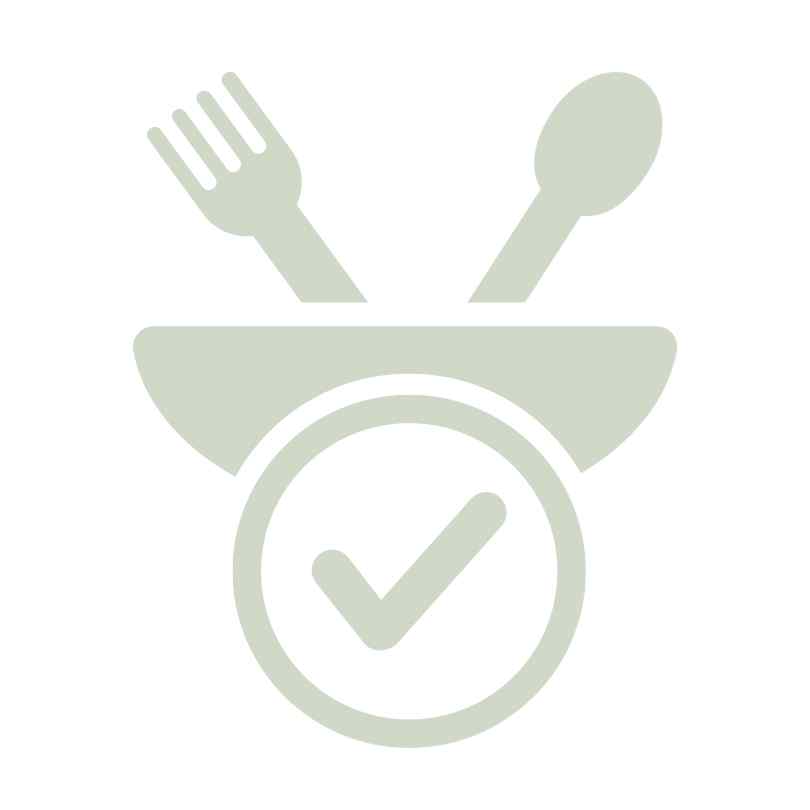
HEALTH AND SAFETY OF OUR CUSTOMERS AND CONSUMERS. Because food safety is a crucial issue for our customers and consumers, we are committed to supplying safe, healthy packaging that complies with every standard.
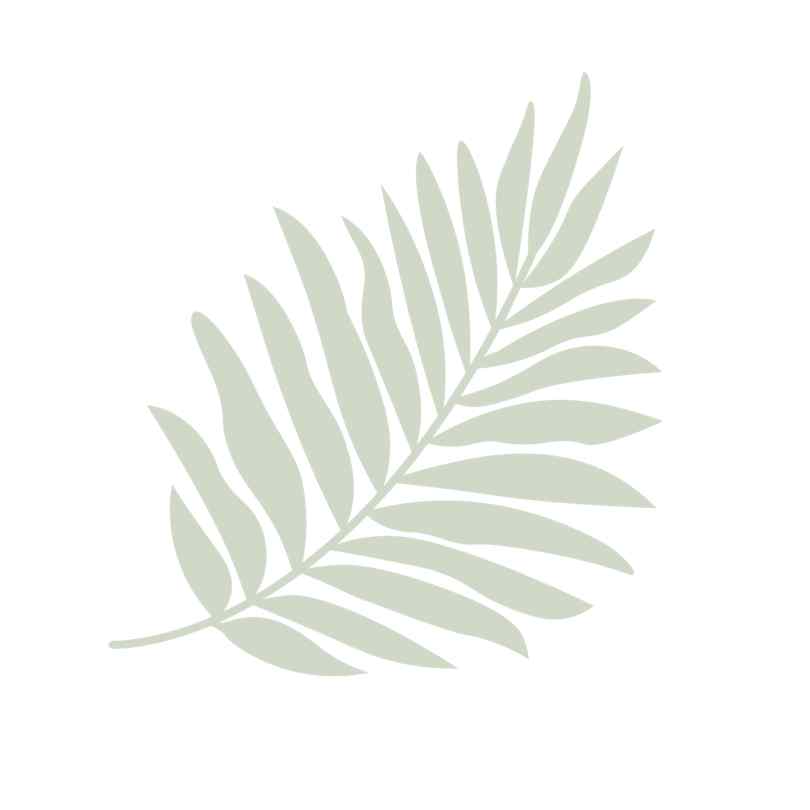
CONTROLLING OUR IMPACT ON THE ENVIRONMENT. We are committed to a sustainable production model, which means monitoring the carbon footprint of our activities. We work every day to try and follow a low-carbon path.
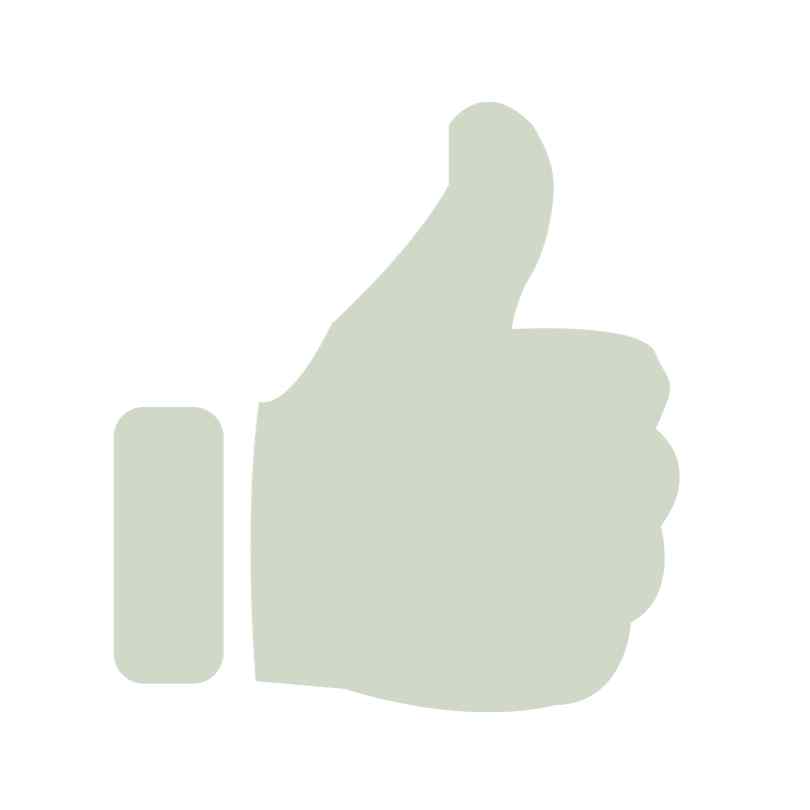
EMPLOYEE WELL-BEING We believe that involving our employees in the company’s success is a key to that success.. Our site and department managers support the professional development of their teams with the backing of HR.
Ecodesign
CREATING APPROPRIATE, RESPONSIBLE PACKAGING
Our R&D and our sales departments work with customers on eco-designed packaging. Recyclability, reduced use of raw materials, new technologies, new materials: these are all areas that have long been and still are the focus of our developments today.
Our approach to ecodesign takes account of the environmental aspects at every stage of the process. It is focused on 4 main areas:
- Selection of the material best suited to the requirements of the target product: our know-how in wood, cardboard, plastic and cellulose packaging means we are able to advise and propose innovative, differentiating solutions.
- Reducing weight: we seek to keep the amount of material used to a minimum whilst maintaining the functionalities of the packaging (conservation, protection, information).
- Mono-material: we prioritise mono-material packaging solutions whenever possible to avoid disrupting sorting streams and to facilitate recycling.
- Inclusion of recycled material: we offer solutions incorporating recycled materials in the cardboard and plastic to save resources and move towards a circular economy.
Our packaging products meet requirements on dual fronts: suitability for food contact and the environmental aspects. By designing entirely recyclable solutions and supporting our customers to choose the most appropriate packaging, we have placed ecodesign at the heart of our business.
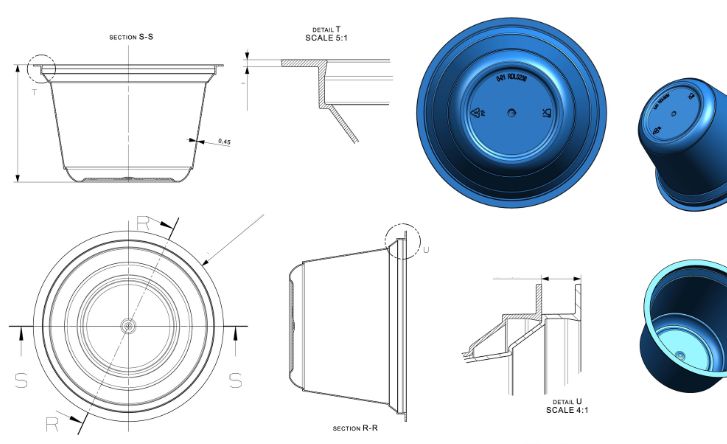
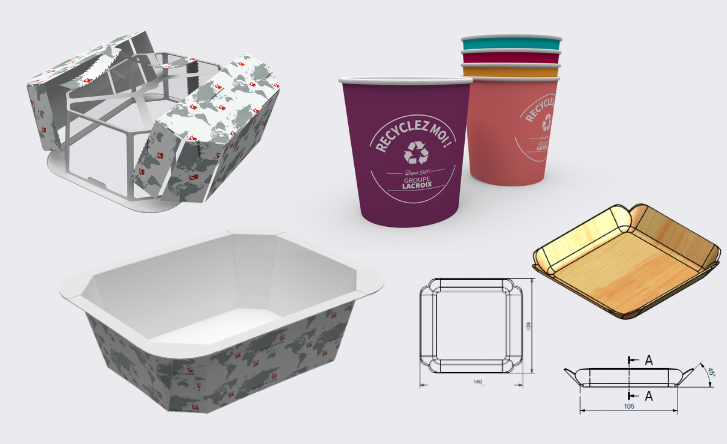
Health and food safety
FOOD SAFETY
The agri-food sector is a complex market, involving many actors, all of whom are subject to a strict regulatory environment governing the market to ensure consumers are provided with safe, quality food products.
Back in 2013, we introduced an internal food safety policy based on the ISO 22000 standard. Today, the majority of our sites are certified to FSSC 22000 or IMS Ratings, a commitment which ensures that stringent food safety rules apply as of the manufacturing of the packaging.
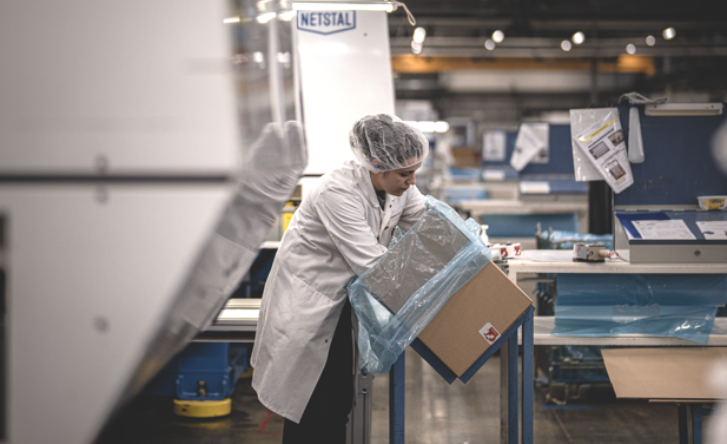
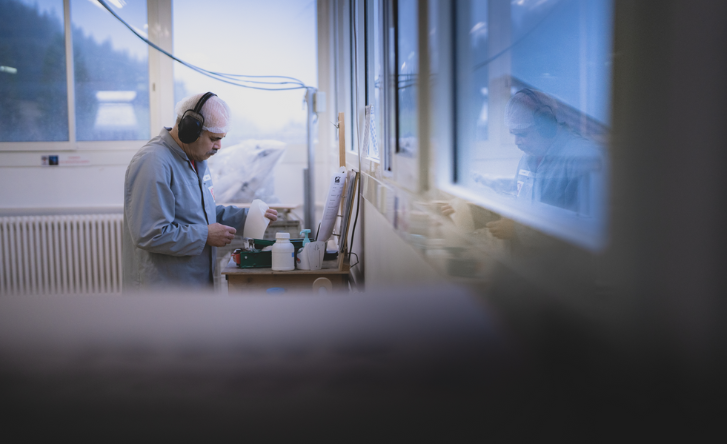
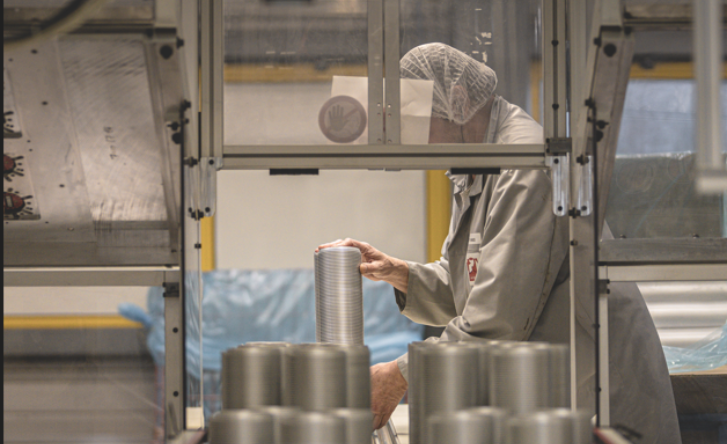
PACKAGING COMPLIANCE
Our goal is to have more than 99% of products that are compliant with food safety standards, and our quality and production departments work together every day achieve that. They guarantee the traceability of our packaging from the raw material through to the finished product. Internal and external quality controls are regularly carried out by our Quality Health Safety and Environment teams. They support and train our operational teams to apply all the latest regulations in order to ensure we provide our customers with safe, compliant packaging.
Controlling our impact on the environment
A CERTIFIED ENVIRONMENTAL APPROACH
The company’s CSR approach has been certified by Ecovadis since 2012.
We are committed to a certified environmental approach that covers all of our activities. Our poplar plantations and our wood processing methods are PEFC-certified. We committed back in 2012 to using sustainably managed timber for our wooden packaging. Our printing shops and assembly sites are FSC®-certified (FSC®C141085) and therefore use responsibly sourced controlled resources. Our French printing shops are certified Imprim’Vert®, which means they are committed to implementing concrete actions to reduce their environmental impact. To be able to offer packaging made from alternative resins, three of our plastic sites, (Ardon, Foncine, St Placide) are ISCC+ certified, which means they can process resins from circular or bio-circular materials. Action has also been taken to prevent and contain plastic pellet spills during handling operations and storage (Operation Clean Sweep).
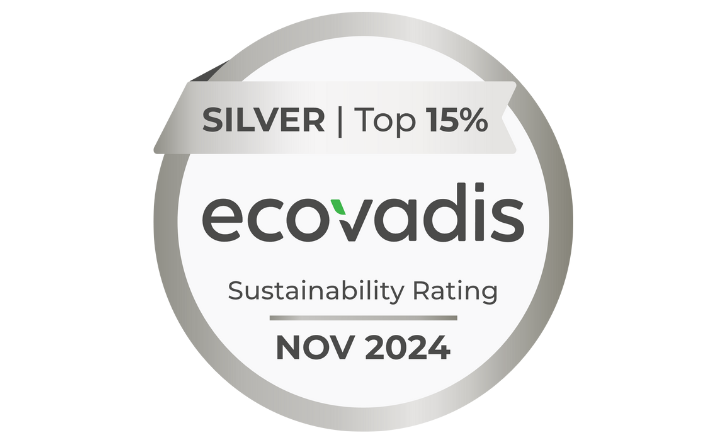
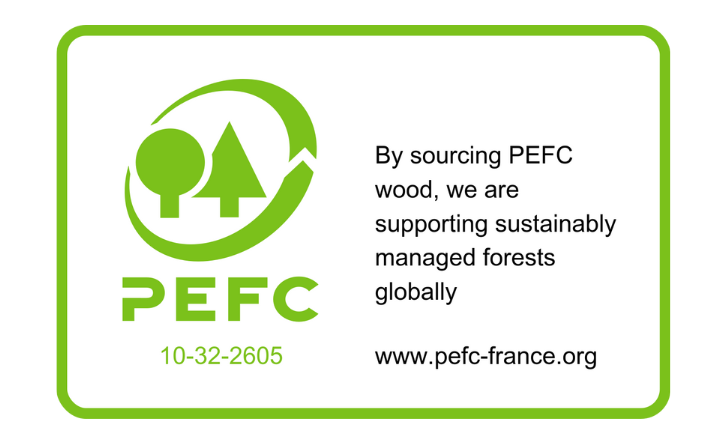
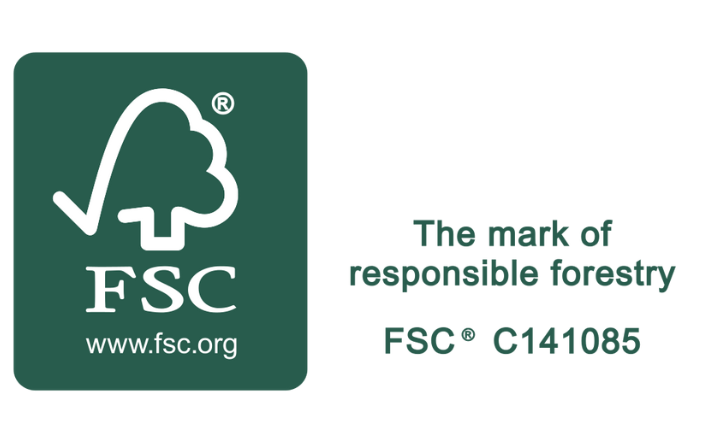
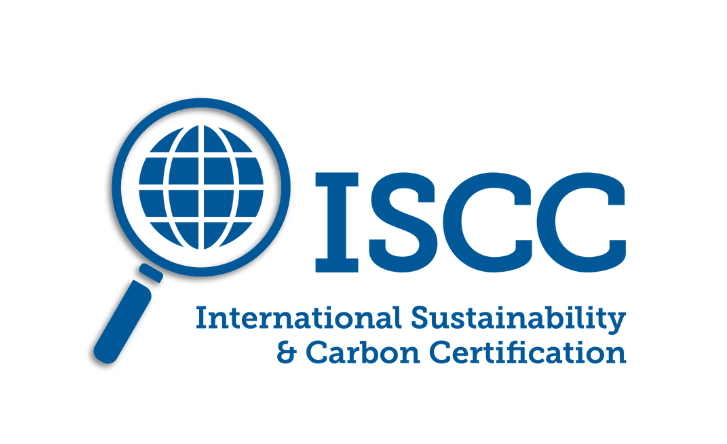
LOW CARBON PATHWAY
As a packaging manufacturer, we are guided by the need to ensure suitability for food contact to guarantee consumer safety and meet our customers’ expectations. Our role in the supply chain requires coordination and close collaboration with our partners. Although we may only have a limited direct influence on scope 3, we nevertheless remain fully committed to minimising our environmental impact, which we do by prioritising sustainable approaches in the design and manufacturing of our packaging products.
Groupe Lacroix has built its low carbon pathway based on 3 strong pillars:
- ecodesign
- closeness to customers,
- energy optimisation.
We measure our carbon footprint (using the Bilan Carbone method of the French ecological transition agency, ADEME) on all 3 scopes as part of our efforts to control our environmental impact. This helps us to measure, manage and improve our low carbon pathway.
ACCELERATING THE GROUP’S ENERGY TRANSITION
We use a variety of levers to manage our energy efficiency. We also monitor our energy consumption on each site. And we have installed systems to recover the waste heat from our production machinery and use it for background heating for our workshops and storage areas. We install photovoltaic solar panels at our sites whenever possible. For example, they were already meeting 75% of our Turkish site’s energy needs in 2022.
Our two veneer peeling sites are both equipped with a biomass boiler enabling them to achieve heating autonomy. These biomass boilers are fuelled with wood waste from our production process. Thanks to these installations, we have been able to make a 43% saving on the energy bill for our French production sites.
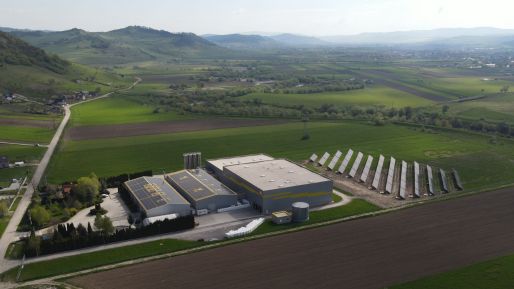
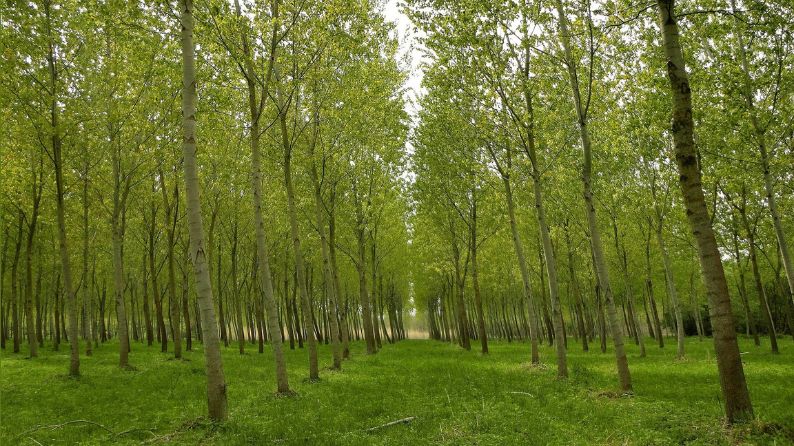
LOCAL PARTNERS
Groupe Lacroix has always made a point of locating its production sites geographically close to its customers. This policy not only allows us to build close relations with them, but it also contributes to the local economy and optimises our supply chain.
A SPECIFIC NEED ? A REQUEST FOR A QUOTATION ?