Our operational departments
At Lacroix Emballages, our operational departments are spread around a number of different sites in France, and their skills and know-how form the core of our business.
Discover how our engineering experts, our creative printing shops and our sustainable poplar plantations contribute to producing quality packaging that combines high tech, creativity and environmental commitment.
Engineering
FROM SPARE PART TO MACHINE
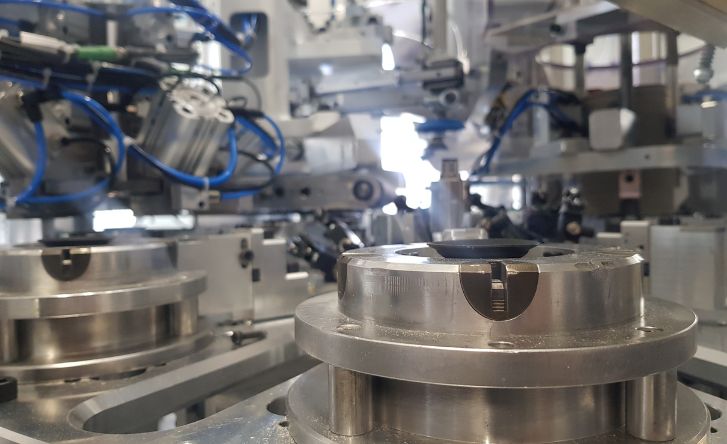
Our engineering department is now spread across several sites:
- Bois d’Amont
- Champagnole
- Souvans
They keep the machines on the sites in perfect working order and develop new production tools.
Why have an engineering department?
At Lacroix Emballages, engineering encompasses a number of trades, including design office technicians, machining operatives, cable fitters, fitters and automation technicians.
From design to manufacturing, our staff are mobilised every day to imagine and work on the new technologies necessary to our development. All this expertise in different areas combined allows us to create, from A to Z, the bespoke machines, moulds and machine tools we need to produce your packaging.
But their job doesn’t stop there. They also provide support and training to other employees across all our sites, to ensure optimum use of new machines when they are installed.
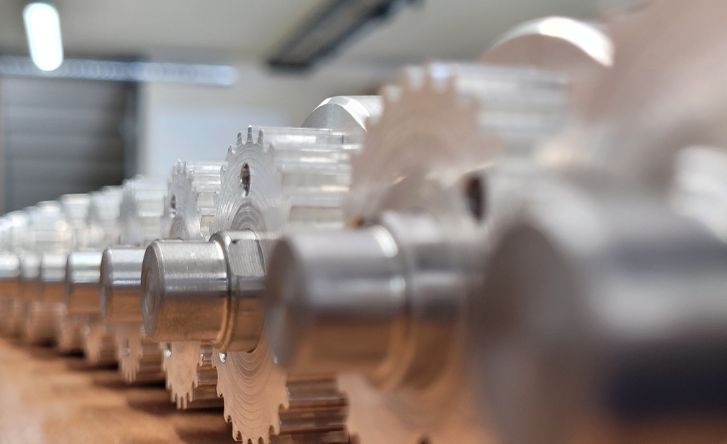
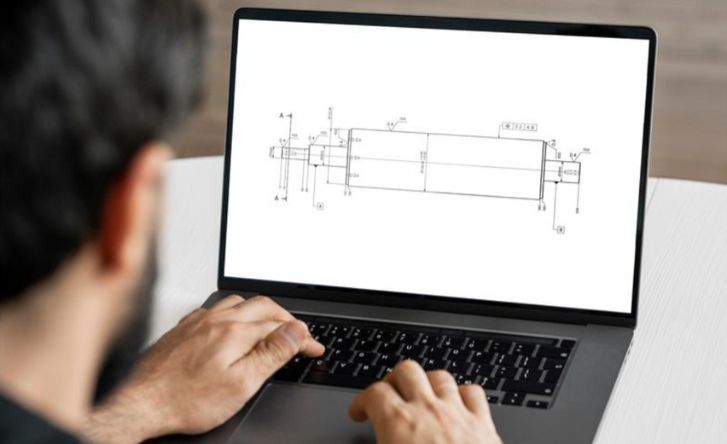
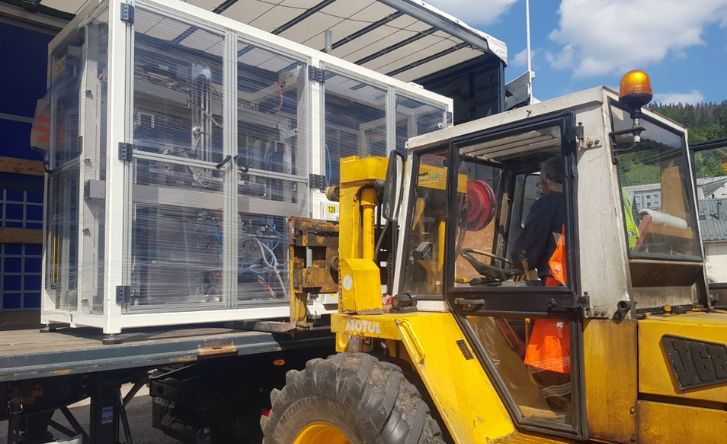
Innovation serving customers and our own teams
We have an in-house engineering department that allows us to control every stage of the manufacturing of our packaging. Our team is involved right from the design of the moulds, which are tailor-made to meet your specific needs. This approach allows us to carry out tests and adjustments in-house without having to rely on external providers.
Our engineering department also plays an essential role in the well-being of our workforce thanks to the work it does to optimise operators’ workstations. The closeness of the staff with the management facilitates communication and allows us to take account of operators’ needs in their routine daily tasks.
As we are constantly taking on board new technologies, we are able to efficiently manage the energy used by our machinery, to heat our workshops and to minimise our impact on the environment.
Production unit
OUR CORE BUSINESS
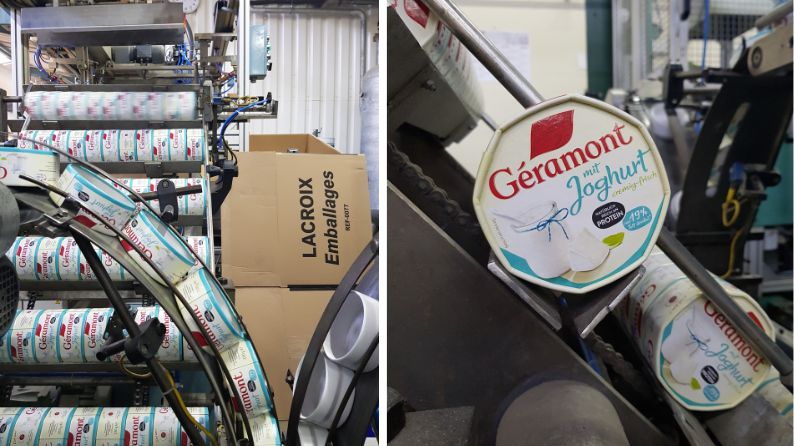
Our production units are the heart of our business and they are strategically located in 11 countries.
All our staff are committed to working every day to produce the packaging you will be using tomorrow.
Sites close to our customers
As our business started out from a small village in Haut-Jura in France, our aim as we developed and grew was to be closer to your production plants. This proximity serves different objectives. The main one is to be able to know and understand your market and its specific characteristics better. But it is also so that we can be more responsive and accessible, thanks to shorter transport times and in-house production.
The corporate culture is also maintained, with small structures situated in often quite rural areas where the number of employees is in most cases about 50. A friendly, family environment is cultivated by a comprehensive management who are close to their workers.
Today, we have 31 production sites spread all over the world, each specialised in a particular field. Assembly of wood or cardboard, plastic injection moulding, printing, veneer peeling, forest management and engineering have become our specialist areas.
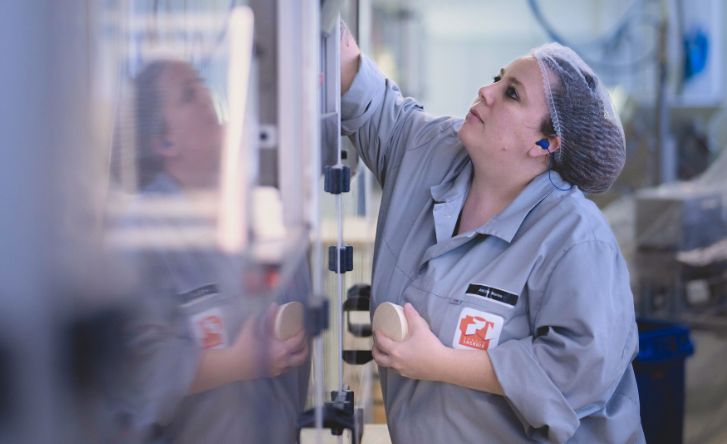
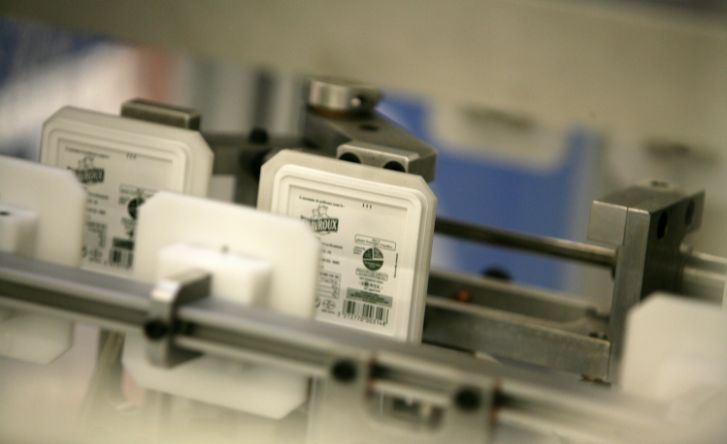
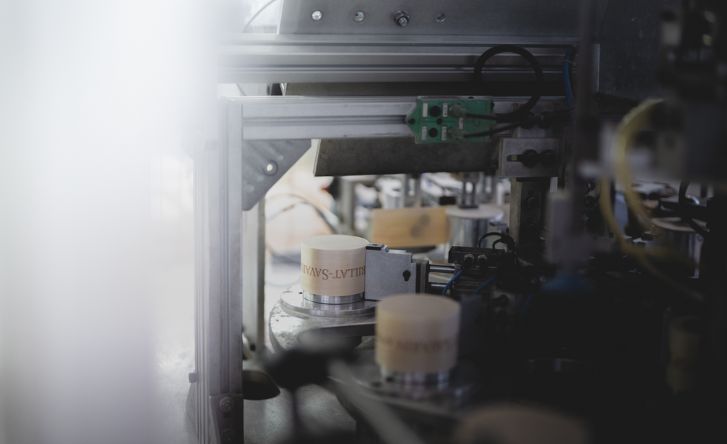
Human commitments and legal obligations
Every item of packaging that leaves our production sites to come to you promises optimum food protection. Thanks to our proximity with your factories and our stock policy, we can undertake to offer you the shortest lead times and meet our commitments on deliveries.
Furthermore, as an environmentally committed company, we manage our energy consumption as efficiently as possible and give our waste a second lease of life by reusing it or sending for recycling.
In addition, many of our sites are FSC® or ISCC-certified, which testifies to our overall commitment to responsible industry. Our teams on all the sites are also trained in the basics of food safety, in line with the FSSC 22000 food safety certification.
Printing shops
HIGH QUALITY CUSTOM PRINTING
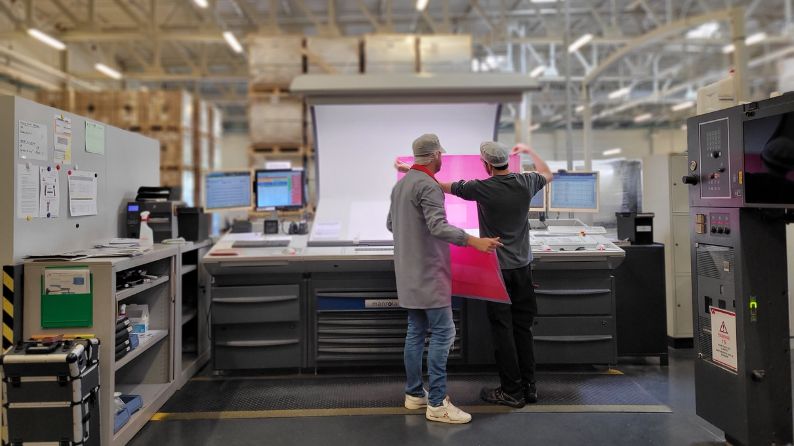
The Lacroix Group’s first printing shop was created in 1975 at Sans-Vallois, with the aim of supplying our other production units.
This was followed by the development of IML printing in Canada in 2006, then at Vittel in 2010, to complete the activity in France.
Creative packaging thanks to our printing shops
Our printing shops are now our main suppliers, allowing us to provide you with custom packaging thanks to two printing techniques:
- Printing on cardboard
- IML printing
As the name suggests, printing on cardboard requires ink and cardboard. Using inks specially designed for food contact and offset printing for the best possible rendering of the visual you have created, printing on cardboard gives you the freedom to be as creative as you want!
IML (In Mould Label) printing consists of inserting a polypropylene label in the mould for your product so that the two fuse together when the material is injected into the mould. This provides high quality printing that is cold, humidity and scratch-resistant, unlike adhesive labels which are in contact with the outside.
Thanks to our expert printing staff, today we are able to offer you high quality, creative packaging solutions, whether it is for direct or indirect packaging such as boxes.
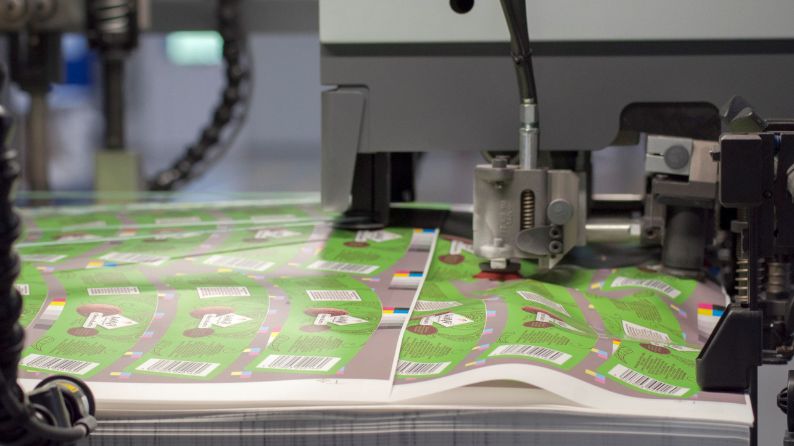
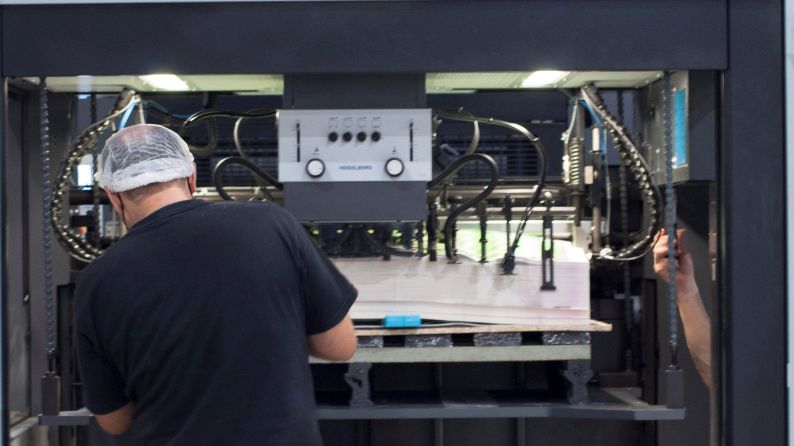
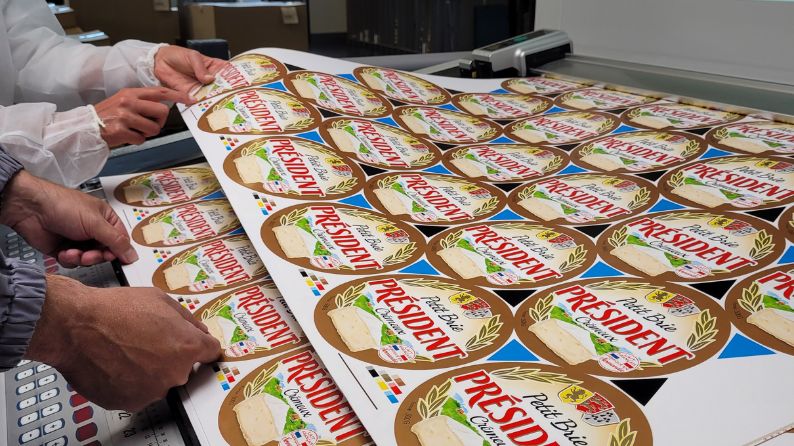
Food safety before all else!
By printing our packaging in-house, we are able to guarantee that the materials we use will not compromise the food safety of your products. We therefore guarantee that we only use non-harmful inks minimising the use of mineral oils and other substances potentially dangerous to health.
At the same time, we are reducing the environmental impact of our business year on year. Our printing shops are in fact certified Imprim’Vert, a certification which promotes responsible practices in the printing process, and we also offer FSC-certified cardboard because we want to contribute to sustainable forest management.
Poplar plantations
FROM RAW MATERIAL TO WOODEN PACKAGING
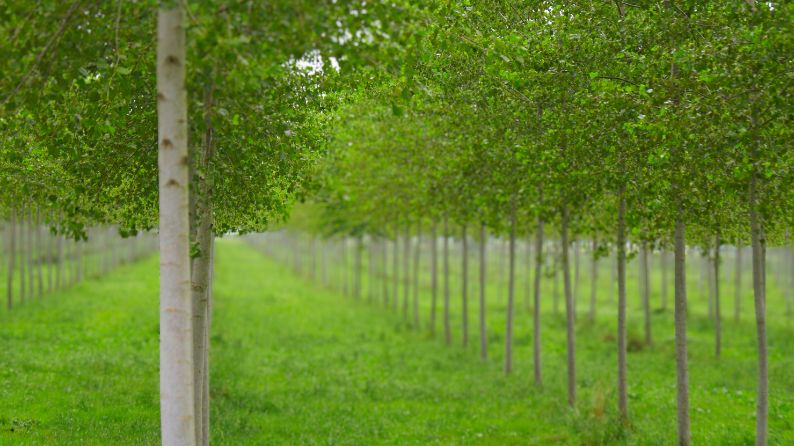
Over the years, our strategy has been to manage part of the production of raw materials in-house.
It was in 2009, that we decided to buy plots of poplar plantations in order to secure our supply of poplar and be able to control the quality of the wood we use.
Sustainability at the heart of our strategy
Our poplar plantations are in the French region of Bourgogne-Franche-Comté, near our veneer peeling sites at Cousance and Branges. Today, they cover 1500 hectares, and 5 people work full time planting, clearing undergrowth and pruning trees.
We chose poplar because it is a strong wood, easy to work and naturally suited to food contact. It is therefore ideal to produce your wooden food trays and boxes.
It also allows us to guarantee our supply of raw material and control the quality of the wood, but also to manage our environmental impact more simply. There are no intermediaries involved in the processing of the timber, no products used that are harmful to the environment or the safety of consumers.
Since 2012, our poplar plantations have been certified PEFC/10-32-2605, which requires us to replant a tree for every tree we cut down. In 2022, we planted 13,152 trees, a ratio of 1.6 poplars planted for each one cut down.
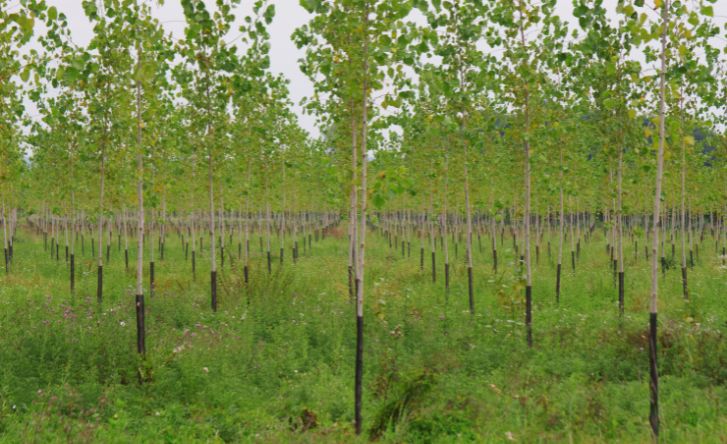
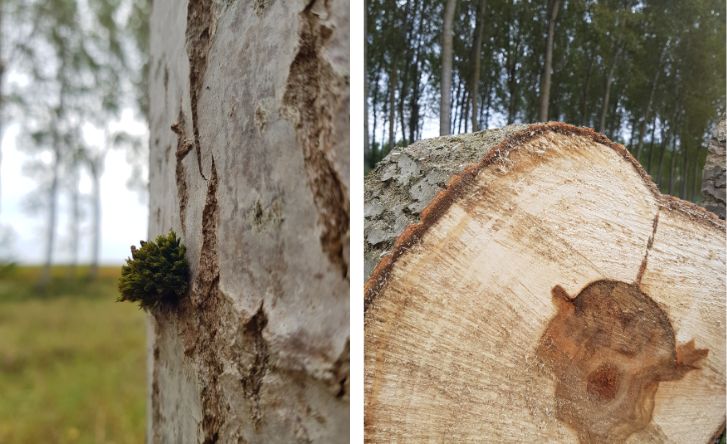

Timber processing on our veneer peeling sites
After harvesting the poplar logs are transported to our two veneer peeling sites.
There they are sorted, cut, debarked and then put through a veneer peeling machine to produce sheets of poplar veneer.
Finally they are oven-dried before going to our production plants as raw materials.
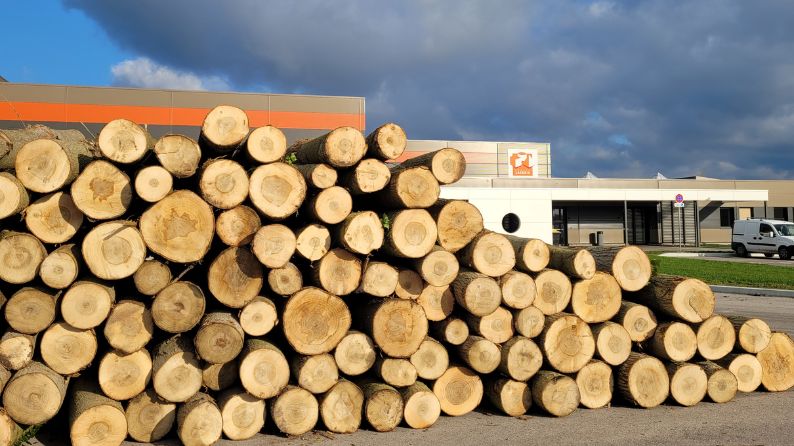
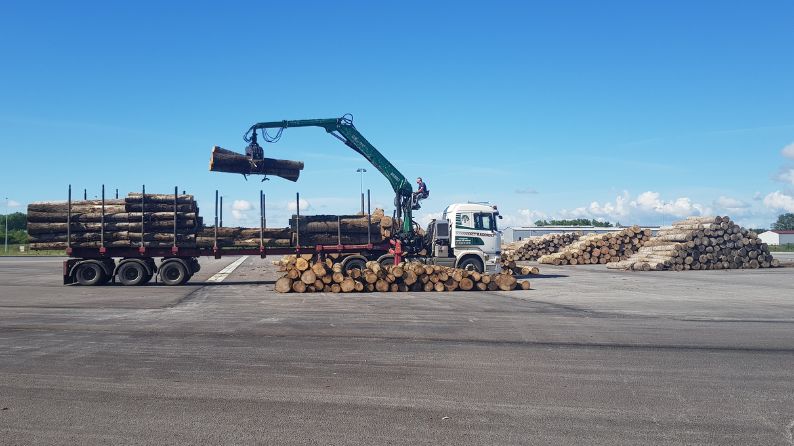
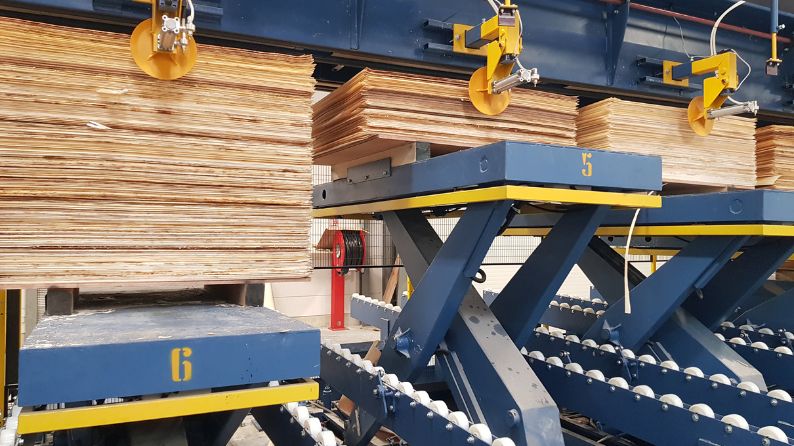